composite span band and where did the ballon nation come from?
In recent years, each of the Spanband and Melt blown markets have faced excess production capacity. Unlike spunbond materials, Melt blowns are made of more discontinuous fibers and are more suitable for applications such as the production of medical masks and sanitary napkins. The similarities between the spunbond and Melt blown materials have not only led to the participation of similar companies in this business, but the tendency to produce composite products by combining these materials has opened another commercial and practical horizon for them. This idea dates back to the 80s. At that time, surgical packages, gowns, sterilization packages and disposable industrial clothing were produced with Spunband composite and Melt blown.
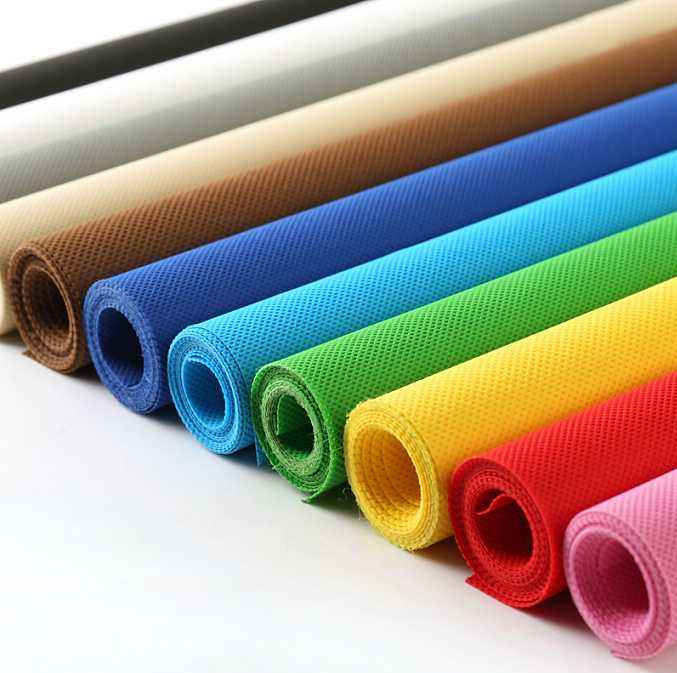
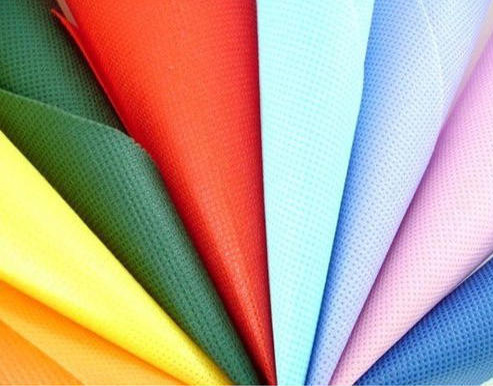